ICD/ITKE Research Pavilion (2017-18)
Team: Prof. Achim Menges, Prof. Jan Knippers, Oliver Bucklin, Marion Lutz, Anja Mader, Evy L.M. Slabbinck, Seiichi Suzuki Erazo, Lauren Vasey, Rasha Alshami, Elaine Bonavia, Brad Elsbury, Samuel Leder, Xun Li, Mathias Maierhofer, Marie Razzhivina, Jacob Russo, Hosna Shayani, Valentina Soana, Sabīne Vecvagare, Ramon Weber, Jacob Zindroski, Israel Luna Miño, Lidia Atanasova, Sven Baur, Ludwig Ebert, Eric Fuertas
Additional Support: Leyla Kyjánek Yunis, Behrooz Tahanzadeh, Michael Preisack, and Maria Yablonina, Larissa Born, Daniel Reist, Daniel Sonntag, Florian Jonas, Bas Rongen, Boris Brozoivc and James Solly
The Institute for Computational Design and Construction (ICD) and the Institute of Building Structures and Structural Design (ITKE) at the University of Stuttgart have continued exploring building-scale fabrication of glass and carbon fiber-reinforced composites. Over the course of two year research and development process, a design was developed for an adaptive, bending-active architectural structure composed of a set of interlocking continuous carbon fiber strip elements. The resulting structure demonstrates the potentials of computational design and simulation technologies in combination with new material processes for innovative and differentiated building scale fabrication.
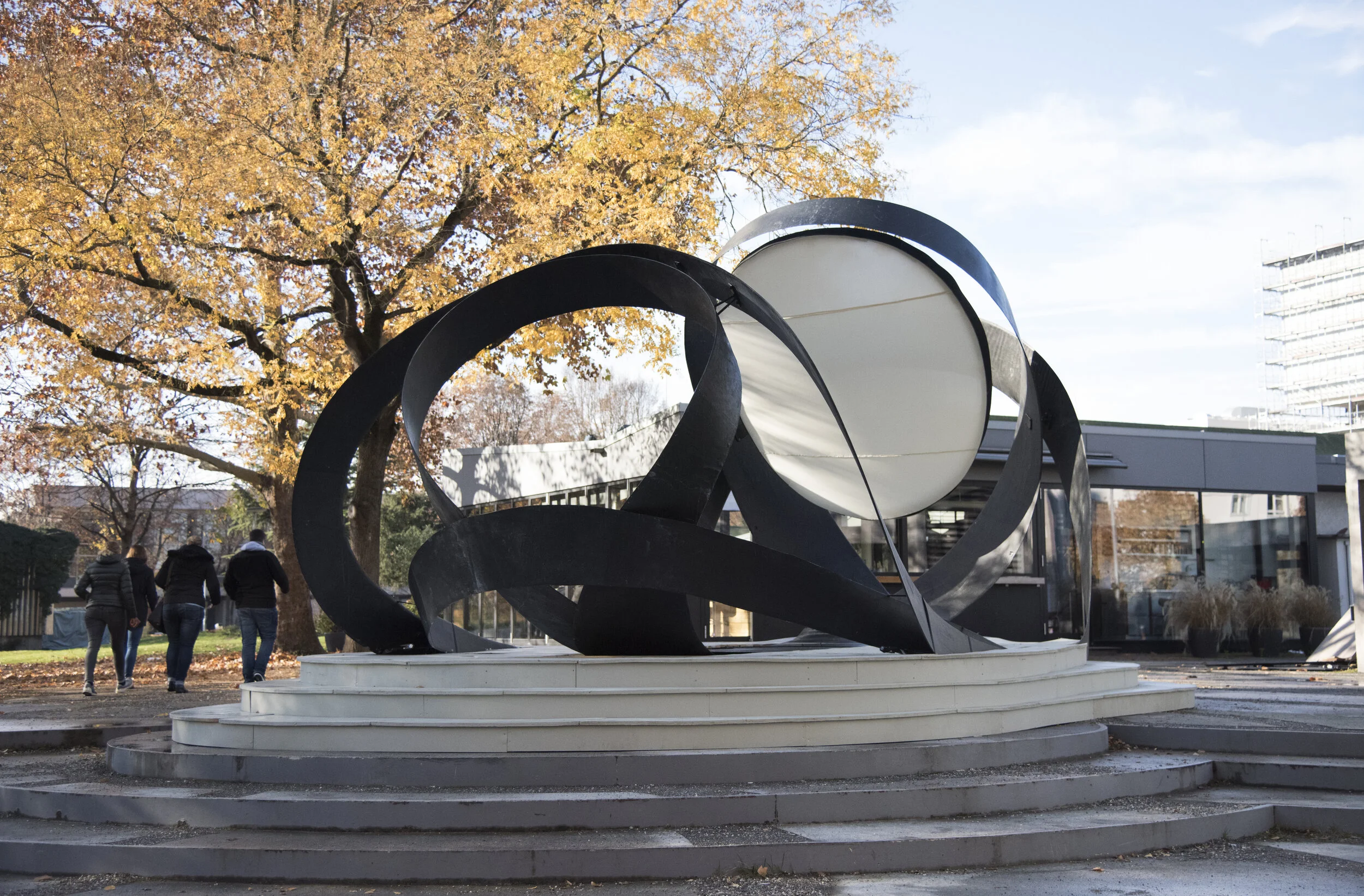


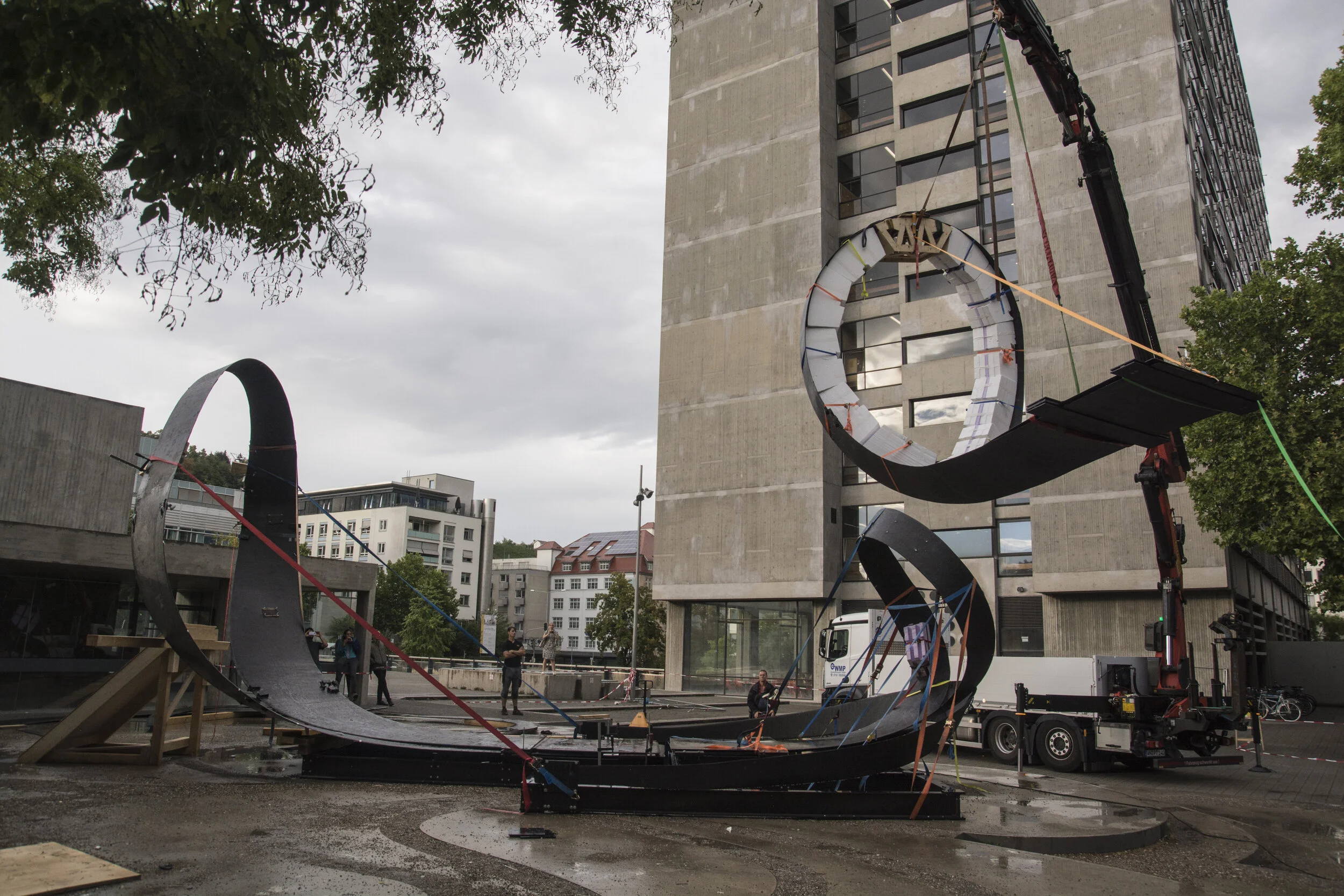


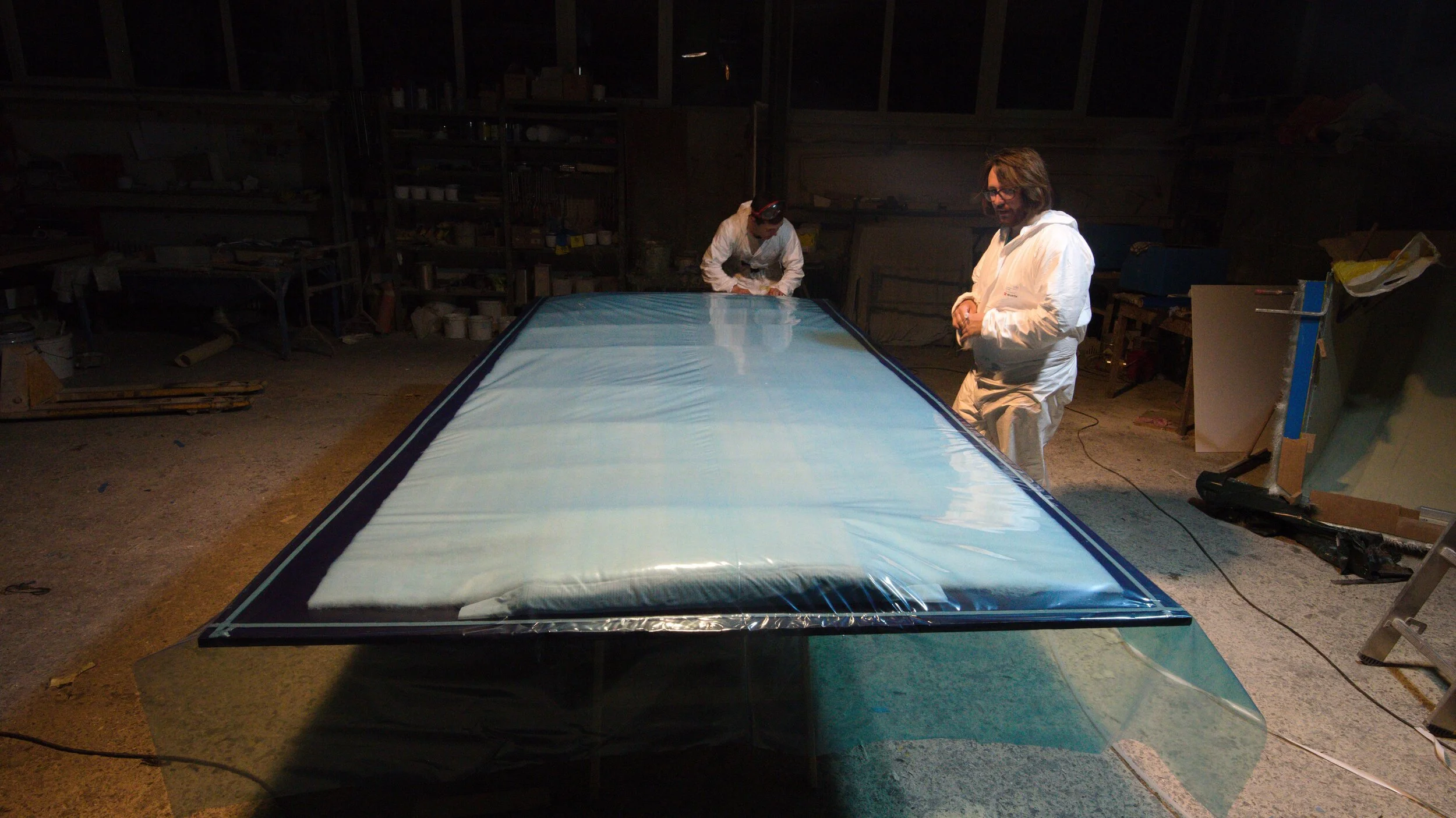
Material System and Development
Fiber composites have enormous potentials in architecture and engineering due to their mechanical properties, in particular their low self weight. Existing fabrication methods for glass and carbon composites implement serialized production methods, limited to the production standardized, identical components. In the building industry and Architecture in particular, there is a need to develop alternate fabrication methods capable of achieving non-standard, differentiated material systems, where material thickness, orientation, and morphology can respond to local mechanical states, desired performances or functions as well as unique site conditions or design intentions. In collaboration with the Institute of Textile Technology, Fiber-based Materials, and Textile Machinery (ITFT), a fabrication process for lamination and vacuum infusion of large scale composite plates was developed. In contrast to fabrication methods where molds or formwork are used, the plates were laminated in a flat two dimensional configuration, and then elastically bent into shape to achieve three dimensional form. Details were developed and tested for fusing multiple plates, enabling the production of continuous large scale components suitable for the scale of architecture.
In tandem to material and fabrication process development, a concept design was developed for an adaptive, bending- active architectural structure utilizing the developed fabrication method. The structure is composed of a set of carbon fiber strips which achieve their stability by interlocking, and included a hybrid membrane, which served a dual purpose to create enclosure and weather protection and to stabilize the structure. This membrane element achieves its unique 3D torsioned shape through prestressing, resulting in a reciprocal equilibrium where all forces are resolved internally.
The design was developed and iterated through a set of computational and form finding tools, including dynamic relation and finite element analysis, enabling design iterations and simultaneous verification. A series of physical material tests at multiple scales helped to benchmark the tools.
The resulting architectural scale pavilion was produced through a combined process of hand lamination and vacuum infusion of a customizable layup of woven carbon fibers, enabling the production of large plates with locally differentiated mechanical properties. Each unique strip was prefabricated in a flat configuration, transported onto site and then elastically bent into shape during an on-site construction process. The interlocking of the separate plates generates a stable doubly-curved geometry, designed to be stiff enough withstand external loading, but flexible enough to enable construction and adaptation. Such possibilities are possible because of the superior mechanical properties of carbon fiber, in particular its modulus of elasticity.